FAQs: ICF Technical
Expereinced builders often pour full storey heights in 2.4 m to 3.0 m lifts to minimise the number of times that a concrete pump needs to be brought to the site. But the bracing required to stabilise the ICF forms of this height and the time required to prepare for the pour can cost more than an extra visit by the concrete pump.
There is very little risk if the first pour height is restricted to 1.2m. Higher lifts can be used in subsequent pours, when the empty ICF forms are stabilised by soldiers that are left fixed to the hard concrete wall beneath them.
Plumbing is really easy in an ICF wall, because vertical and horizontal chases can be cut in the inner leaf of the house wall and the pipework can be installed in these, fixed in place with foam and subsequently covered by the wall finishes.
Service ducts can easily be cast in the walls using 100mm PVC drainage pipes.
In the same way that plumbing as installed as described above.
ICF walls are provided with 150mm and 200mm concrete cores in the UK. Generally, walls extending down to 1.2m below ground and all those above ground are 150mm thick. Retaining walls deeper than 1.2m deep will have 200mm concrete cores.
ICF walls only need waterproofing if they are installed in basements below ground. There is a Code of Practice, BS8102, that deals with this.
The Code provides 3 design grades which defines the acceptable levels of water penetration depending on the usage.
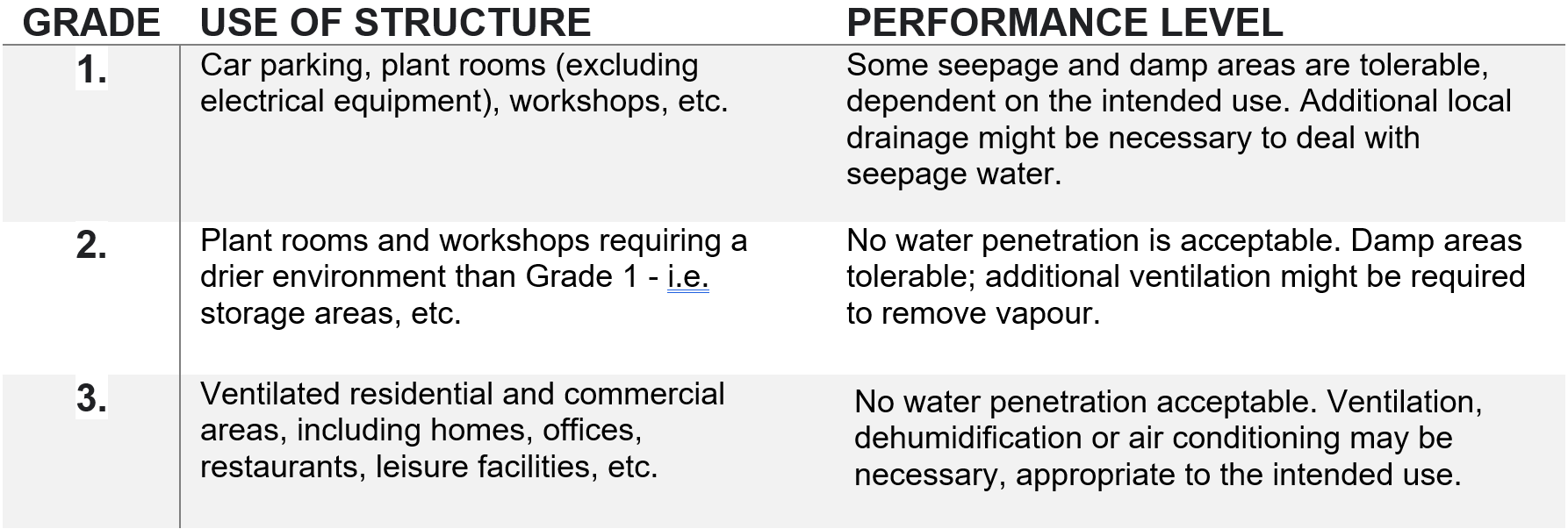
Every basement must be designed by a Chartered Civil or Structural engineer that will advise you on the measures that might be required for waterproofing.
Kitchen and bathroom cabinets can be quite heavily loaded but they be fixed using the ferrule strips.
The load security can be increased by removing the EPS foam over the area of the item to be fixed and screwing 12mm plywood directly to the ferrule strips and then fixing the load to the plywood.
Items like boilers need to be fixed to the concrete core. This can be with fixing bolts with steel tube sleeves or by replaing the EPS with render at the fixing points and using fixing bolts that extend at least 2″ into the concrete core through the render.
Yes, and plasterboard can be fixed by Dot and Dab or by self-tapping screws into the ferrule strips.
ICF Walls are Vapor-Resistant and act as vapor retardants, and so ICF walls do not need vapor barriers. ICF’s have insulation on the exterior and interior of the walls separated by a thermal mass of concrete. The insulation stabilizes the temperature and prevents condensation within the concrete walls.
ICF houses do not need an air barrier as the concrete core itself serves as a very effective air barrier. The June 22 edition of the Building Regulations require every dwelling to be tested for air-tightness before a Compliance Certificate can be issued. This will cause many problems for traditional and timber frame construction but with ICF the only issue is that it may be necessary to add an air barrier around windows and door frames, sealing them to the ICF wall.
Find out more about energy efficiency in ICF.
ICF structures are more resistant to disaster, fire, insect and moisture intrusion than wood-frame buildings. They also provide a more thermo-efficient, noise reducing, and healthy building than wood structures. Furthermore, it is virtually unknown for houses built in ICF to crack because of subsidence.
ICF is made of non-toxic materials, thereby creating a healthy interior environment. Without air infiltration, the occupants are not bothered by dust or allergens and there are no cavity walls for mould, mildew, insects or rodents to infest.
ICF Construction
Call us if you need more detailed information for your ICF project, browse our technical library and FAQs for construction details using Polybloks.